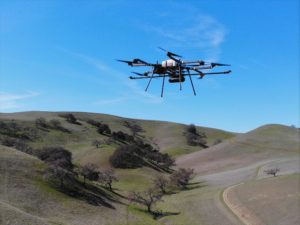
Used for creating precise 3D models of terrain for mapping and more, LiDAR surveys are an important commercial application for the drone industry – but battery limitations and the associated short flight times remain a problem. Now, California-based Skyfront is working with European UAV LiDAR solution provider Routescene to explore the impact of increasing flight endurance, using Skyfront’s Perimeter 8 gasoline-electric hybrid multicopter.
Drone battery life is a problem for all commercial drone operations: but when combined with the weight of LiDAR sensors, flight endurance can be severely affected. “Typically a drone utilising lithium polymer batteries, such as a DJI M600, and carrying a 3.3kg payload (for example a Routescene UAV LiDAR system) would operate with a flight time of around 15-20 minutes,” says a press release. “Landing, replacing the batteries and take-off between each flight can take longer than the flight itself, directly influencing the size of the survey area that can be flown each day.”
The impact of reducing downtime in LiDAR surveys
For larger LiDAR survey sites that might require more than one take-off and landing site, the limited flight time can lead to significant downtime – which costs signficant money. Teams from Skyfront and Routescene set out to demonstrate that increasing flight time by using a hybrid fueled drone could signficantly impact data collection productivity.
The results were an impressive 3 hour flight time for the Skyfront Perimeter 8 carrying a Routescene LiDAR payload: reducing downtime so significantly that a typical 2-day project could be completed in one day. “The Skyfront Perimeter 8 is an eight rotor hybrid UAV designed for carrying heavier payloads such as LiDAR. The Perimeter 8 has both rotor and complete engine redundancy for safety,” explains the release.
Gert Riemersma, Founder and CTO of Routescene, commented, “Through this testing the team found the greatest benefit gained was regarding efficiency. Due to the longer flight times, only one take-off and landing site was required, removing the need to travel between sites to repeatedly set up. In addition, a considerable amount of time was saved simply by eradicating turn-around times to replace batteries. We estimated that by achieving 3 hours of flight time at 5m/s you can readily cover 54 survey line kilometres, or just over 500 acres. This is equivalent to roughly 10 x M600 flights, which would normally take two days to complete. An impressive result, reducing two days of surveying into less than one day, simply by eliminating downtime.”
The Routescene UAV LiDAR system has a solid state disc onboard capable of storing over 13 hours worth of data, “more than enough for a full day in the field,” explains the team. “The quality of the data being collected is monitored in real-time during the entire drone survey using Routescene’s QA Monitor, a web based app, to make sure you leave the survey site with the data you need. At the end of the survey the data can be downloaded and checked in the field using Routescene’s LidarViewer Pro data processing software.”
Gert added, “Routescene has a strong ethos of quality assurance and quality control (QA/QC). Implementing rigorous QA/QC improves data quality and efficiencies. QA Monitor gives you confidence in the data you are collecting while you are collecting it. The last thing you want after completing a long survey flight is to realise there was an issue and the team has to mobilise to fly the area again. It prevents time being wasted, you can identify an issue immediately, remedy it there and then in the field, bringing further efficiencies to the increased gains brought by longer flight times.”
Longer flight times don’t only increase productivity – they have a positive impact on safety too. “The riskiest parts of a UAV flight are the take-offs and landings, when the drone is under manual control and hence when accidents are most likely to occur. Reducing the number of take-offs and landings obviously directly reduces the probability of an accident,” says Skyfront.
Brian Maxwell, VP of Business Development at Skyfront, confirmed, “Our flight time of 3 hours was particularly impressive and allowed a huge volume of 3D data to be collected efficiently. We found that we could considerably improve the resilience, efficiency and safety of UAV LiDAR surveys by increasing the flight time.”
Christian Andresen from the University of Wisconsin added, “In 2017 and 2018 we surveyed areas of the Arctic as part of the NGEE Arctic project researching changes to permafrost and ecosystem structure. What we observed over the 2 years whilst working there was how much drone technology improved and the positive impact that had on flight times. The Arctic location was exceptionally remote and all incremental improvements make a huge difference to our efficiency and reduce time spent in the field. A drone that could fly for 3 hours would make a dramatic difference for our future surveys in this remote area.”
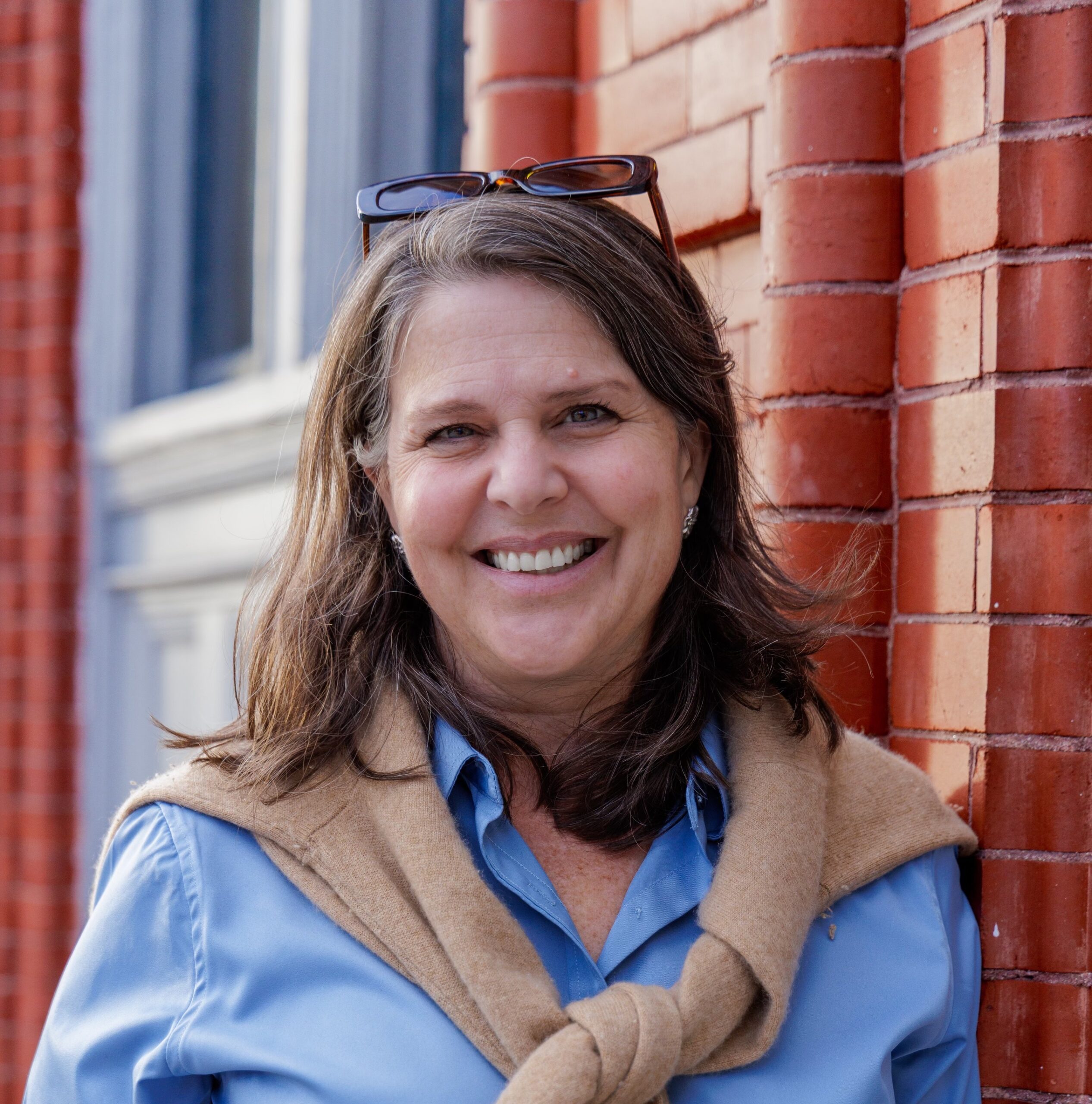
Miriam McNabb is the Editor-in-Chief of DRONELIFE and CEO of JobForDrones, a professional drone services marketplace, and a fascinated observer of the emerging drone industry and the regulatory environment for drones. Miriam has penned over 3,000 articles focused on the commercial drone space and is an international speaker and recognized figure in the industry. Miriam has a degree from the University of Chicago and over 20 years of experience in high tech sales and marketing for new technologies.
For drone industry consulting or writing, Email Miriam.
TWITTER:@spaldingbarker
Subscribe to DroneLife here.
[…] California-based Skyfront is collaborating with Routescene to explore the impact of increasing flight endurance, using […]