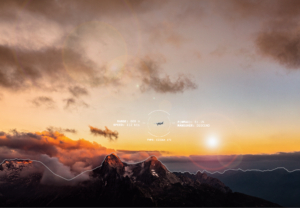
BVLOS is something the drone industry has been waiting for. Michael Huerta, then FAA Administrator told an audience in January of 2017 that a rule on BVLOS flight was one of his primary objectives for the year. A rule has been slow to appear, however. DRONELIFE spoke with Iris Automation CEO Alex Harmsen about Iris’ onboard sense and avoid technology – and building trust with regulators.
So far, the FAA has issued BVLOS waivers – but they are often not scalable operations beyond line of sight. Some BVLOS waivers require ground radar along the entire flight path: others require that visual observers “daisy chain” along the route. Some represent an “extended” range of operation from the operator, without realizing the potential of true distance operations.
Waivers that require multiple visual observers along the route or a ground based radar system, however, don’t actually help to evaluate potential operations like long line linear infrastructure inspections; or scalable package delivery. The test scenarios are about building trust with the FAA; but in terms of the real commercial applications, Harmsen says, “They don’t make sense… they don’t solve the fundamental problem of making those applications more efficient.” That’s a real limitation for the industry, Harmsen says: “The main reason that drones haven’t exploded in industry the way that people expect them to is that this problem hadn’t been solved.”
Onboard Detect and Avoid
If you don’t have a human being watching the sky, or install a ground-based system all along a flight route to identify birds, other aerial vehicles, and any additional air traffic: how do you ensure that drones will be able to avoid obstacles moving into their path? The answer, says Harmsen, is an onboard detect and avoid system. It’s a computer vision system that allows an unmanned system to “see” where it’s going, adjusting a flight path automatically to avoid conflicts in the way. Since it doesn’t require permanent infrastructure or additional staff, “We see this as the only scalable way to solve this problem,” says Harmsen.
“It’s taken us about 4 and a half years to build and get approval for the systems that we’re working on now,” says Harmsen. “It’s incredibly difficult, it takes a lot of upfront investment.” Harmsen explains that drones flown within visual line of sight operate similarly to small manned aircraft. “There is air traffic control around certain airports, but most of the airspace is Class G or Class E airspace – and we trust aircraft to fly wherever they want there, because we trust the pilots to see and avoid any other traffic.”
Detect, Track and Classify
“That’s exactly the same things that our system does,” Harmsen explains. “We’re looking at a potential 500 objects at a time and classifying them.” Detect, track, and classify – the system captures what a potential conflict looks like, how it moves, and then determines a classification: “It’s a lot more likely that we’re going to encounter birds than other aircraft,” says Harmsen. “Then we do trajectory planning and take evasive action – and all of that happens in milliseconds.”
Currently, Iris Automation is working with the Kansas Department of Transportation with an FAA BVLOS waiver: the company expects more waivers currently in the works to be approved within the next few months. Iris is also involved with developing an ASTM standard for BVLOS flight. These are all necessary steps towards making BVLOS flight standard. “We’ve seen this same sort of scenario play out with other operations,” says Harmsen. “There may be a couple of initial BVLOS approvals that can set a precedent; then there is a standard that comes out from industry; then there is an official rulemaking.”
Efficient, inexpensive BVLOS flight will be a game changer for the industry – and Harmsen says that it’s now possible. “There are other ways to get to BVLOS, but they’re just not scalable,” he says. “There is a huge improvement in having a system onboard.”
“This is a time for us to raise the tide for the entire industry – so many people have been waiting for this.”
Miriam McNabb is the Editor-in-Chief of DRONELIFE and CEO of JobForDrones, a professional drone services marketplace, and a fascinated observer of the emerging drone industry and the regulatory environment for drones. Miriam has penned over 3,000 articles focused on the commercial drone space and is an international speaker and recognized figure in the industry. Miriam has a degree from the University of Chicago and over 20 years of experience in high tech sales and marketing for new technologies.
For drone industry consulting or writing, Email Miriam.
TWITTER:@spaldingbarker
Subscribe to DroneLife here.